Quick reaction to market fluctuations and flexible manufacturing capabilities have helped many Taiwanese manufacturers of machining centers to escape the impact of economic recession in major markets.Those markets include mainland China,which is the world's second-largest economy and the biggest buyer of made-in-Taiwan machine tools,including machining centers.
Taiwan is the world's No.4 exporter of machine tools.Now,however,it is losing ground to emerging mainland Chinese machinery manufacturers in the middle and low ends of the market,where it has been dominant for some time,and local manufacturers do not want to compete with German,Japanese,and Italian suppliers in the market for high-end standard machines.Instead,they are striving to develop high-value-added machines for special purposes.These are machines that,because of their limited market demand,big Western suppliers are not interested in;at the same time,Chinese competitors are still too immature to compete in this segment of the market.
The niche machines that Taiwanese manufacturers are developing are designed mainly to make molds for precision parts used in consumer electronics,computer and communications(3C)equipment,medical equipment,aircraft,vehicles,gas pipes,and wind turbines,among other products.
In developed markets,Taiwan-made machining centers are well received because of their high performance/price ratio,which allows Western manufacturers to maintain production quality at a relatively low cost at a time when the global economic outlook remains hazy.
These niche machines reflect international trends with features such as multi-tasking,an A-shaped mechanical structure,high-speed main spindle,high-speed feed rate,precision ball bearings,high-speed and high-precision ballscrews,high-performance servo motors,and CNC software.
One of the local makers of niche machine tools is the CNC-TAKANG Co.,which develops machining centers with A-shaped body structures in line with the latest international trend."Structurally,this design is conducive to the rapid dissipation of heat,which is generated mainly by the main spindle cutting hard components,"explains the company's technical director,C.C.Chen,who has been in the industry for more than three decades."This considerably minimizes cutting error caused by overheating.Also,this design evenly spreads the weight on the machines,further reducing vibration during operation."
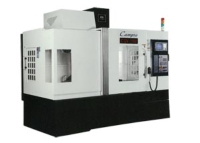
Controlling Heat
Chen notes that metal normally expands under high temperatures,and that this can spoil the accuracy of a machine.Before developing the double-slant A-shaped structure,he says,his company developed designs that keep the temperature of the main spindle to within 10 to 12 C above ambient temperature.
The company will roll out its double-slant machines at the Taipei International Machine Tool Show 2013,which will be staged on March 5-10.
Founded in 1972,CNC-TAKANG specializes in machines for the heavy-duty machining of hard,massive components used in vessels,automobiles,aircraft,wind-power equipment,and oil-refinery equipment.With ISO9002,CE Mark,and New CE Mark certifications,the company's heavy-duty machines cut work pieces with a spin rate of three to 600 RPMs per minute.
The company avoids mass-producing standard types of machines."Instead,"Chen explains,"we make tailor-made machines for special purposes,which command pretty good profits but are not attractive to the big-name manufacturers who are competing to maximize their dominance of the market for standard machines with huge demand."
As a result,Chen claims,his company has not felt much impact from the recession that has afflicted most markets.In fact,he predicts a sales growth of 10-20%this year."Unlike buyers of light-duty equipment,"he comments,"buyers of heavy-duty equipment usually carry out expansions during downturns to take advantage of the relatively low cost of credit."
The company is also following international trends by developing multi-task machine tools,which combine the functions of machining centers and lathes."This type of machine does not do just drilling,milling,and boring,but also lathing,"Chen explains.This is in line with the demand for machines that can do all of these machining tasks on large,heavy work pieces in a single setup,saving the energy and time of loading and unloading work pieces from one single-task machine to another.
Chen is proud of the accuracy that his company's machines provide,giving two examples to justify his pride.One concerns machines that the Dongfeng Motor Corp.of mainland China ordered to make camshafts,the other machines for making main shafts for hydropower turbines."In the Dongfeng case,"he says,"our machines guaranteed no more than a 0.05mm eccentric deviation on the camshafts,much lower than the 0.22mm that a Japanese equipment supplier promised."In the turbine shaft case,the company's machines provided a maximum deviation of 0.005mm from true round on the 600mm-diameter,six-meter-long shafts.
CNC-TAKANG has supplied its machines to mainland Chinese automakers FAW Group Corp.and Dongfeng Peugeot Citroen Automobile Co.,as well as Dongfeng Motor.The first customer for the company's automated production line,however,was Taiwan's Ford Lio Ho Motor Co.,which installed it to make brake drums in 1987.
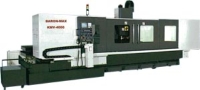
Providing Flexibility
To keep up with rapid model changes,the company's machines allow carmakers to switch jig tools and software programs to fit new models."In the past,"Chen notes,"carmakers usually had to change machines when they wanted to introduce new car models.At that time,the designs of machine tools lacked flexibility."
CNC-TAKANG ships its machines mostly to Europe,the United States,Russia,India,Turkey,the Middle East,Latin America,mainland China,and Southeast Asia.In Europe,the machines are available under buyers'brand names;in other markets,they carry the"CNC-TANKANG"brand.
Another top supplier in the line is the Campro Precision Machinery Co.,which makes vertical machining centers,horizontal machining centers,CNC lathes,CNC turning centers,CNC double column machining centers,and CNC traveling column machining centers for various industries,including those making molds for the 3C(consumer electronics,communications and computers)component,aircraft,car-component,motorbike-component,oil-equipment,and optical-component industries.
This year,equipment for 3C industries will be a major revenue booster for the company,according to sales manager Kevin Mao."We forecast that our revenue will rise 50%this year,mostly thanks to 3C equipment sales,"Mao explains."But even without sales of 3C machinery,our revenue for this year would still be on a par with last year's,since as of the third quarter we have secured orders that equate to our total for all of 2011."This year's expected growth rate,he says,is the strongest since the company was founded eight years ago.
Campro's CQV series 3-axis vertical machining centers are typical of the company's machines for making 3C-component molds and molds for other industries.This family comes in CQV1300,CQV1100 and CQV900 models,the numbers of which denote X-axis travel length.
Y-axis travel for both the CQV900 and CQV1100 is 580mm,while for the CQV1300 it is 600mm.Z-axis travel length for all three is 560mm,and all have an 11kW or 13kW spindle.
The company's machines have been installed by numerous silicon-wafer fabs,mobile-phone case makers,LED module makers,TFT LCD module makers,and makers of car parts all over the world.
Asked about Compro's competitive advantages,Mao came up with a long list:"Our machines are more rigid than most competing products,our main spindles are better than most,we have our own in-house R&D unit,we do our own quality control,and we do most of the assembly ourselves.We also have coordinated measuring machines,which are edge examination tools that many local machinery manufacturers still do not have."
The company makes its machines in accordance with Japan's JIS and Europe's VDI 3441 standards,qualifying them for sale in most developed markets."To assure that as few environmental conditions as possible affect the quality of our machines,"Mao emphasizes,"we assemble them in air-conditioned buildings.And we examine each outsourced component and piece of material with coordinate measuring machines for precision of specifications."
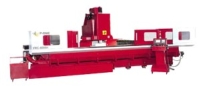
Avoiding Standard Products
Like many of its local peers,Campro avoids making standard machines in large volumes so as to avoid competition with bit international players.The company now hopes to increase the value of its products by developing 5-axis double-column machining centers.
Mao is supremely confident of his company's technical capabilities,citing the management team's average 25 years of experience in the machine tool line."That's why we have been able to introduce 50 models of machines in just eight years,"he says.The own-brand machines are marketed through 30 dealers worldwide.
Koan Cho Machinery Co.was founded in 1976 in Taichung,central Taiwan,to make vertical machining centers,horizontal machining centers,vertical milling centers,graphite milling centers,CNC rigid bed mills,tool room CNC bed milling machines,CNC combination lathes,and heavy-duty CNC lathes.The machines are designed for use in the oil-pipe,car-part,aircraft-part,rail-track,medical-component,fitness-equipment,and 3C-component industries.
A typical example of the company's popular products is its KMV family of traveling column machining centers,which come in KMV-4000,KMV-5000,KMV-6000,and KMV-7000 models designed for heavy-duty cutting,on work pieces such as rail tracks and H beams,with a traveling column and fixed table.The machines have X-axis travel of 4,000mm,5,000mm,6,000mm,and 7,000mm,respectively,as indicated by their model numbers.Y-and Z-axis travel is 600mm.
A CE-certified manufacturer,Koan Cho ships its machines mostly to Russia,Brazil,the Middle East,Turkey,the United States,and Canada.To assure quality,the company uses cutters from Japan,Germany,or Switzerland,and control units from Japan,Germany,or France.And,stresses managing director Mentor Lin,"Our engineers are responsible for the development of drive software for our PLC-based control units."Some of the machines from his company,he says,are used by contract suppliers for Boeing.
The company sells products under its own brand name,"BARON-MAX,"and provides contract manufacturing as well.Lin is especially happy about the latter operation."Tailoring machines to meet the specific needs of different customers is our strength,"he says."And that's why our machine models are so diversified."Lin adds that the tailoring focuses mainly on details of mechanical structure,and that the company guarantees delivery in two to three months for each contract order.Koan Cho is now developing 5-axis machining tools for making aircraft parts.
The P-ONE Machinery Co.,a contract manufacturer of machine tools,is especially good at making both vertical and horizontal machining centers for light-duty cutting purposes.The machines are ideal for making moulds for small car and aircraft parts.
Among the 11-year-old company's star horizontal machining tools is the 3-axis HMC-1000,with 1,000mm of linear axis travel in X,750mm in Y,and 600mm in Z.Its rotary square worktable measures 1100mm x 600mm,and the machine is outfitted with an 11/15kW 7000rpm spindle.
Ensuring Accuracy
Each HMC-1000 is laser calibrated,ballbar tested,and subjected to dynamic machining to ensure cutting accuracy.The machine utilizes a highly malleable casting approach combined with a rigorous scrapping technique,highly rigid structure,and highly precise axial feeding system to ensure precision machining.
The machine has a control panel fixed on a suspending bar so that it can be moved forward and backward,and rotated 180 degrees,for the convenience of the operator.The Internet-connected control unit sends a real-time machining video feed to customers'computer monitors.
The VMC-4000H traveling-column machining center,another popular P-ONE product,is designed primarily for working with strip-and panel-shaped iron and aluminum work pieces such as rail tracks.This 3-axis machine's linear axis travels 4,000mm in X,450mm in Y,and 500mm in Z,and it has a BT40 10,000rpm spindle.
The travel distance of the spindles can be extended to 5,000mm,6,000mm,7,000mm,8,000mm,9,000mm,or 10,000mm,depending on customer needs.
According to P-ONE's general manager,L.W.Chiang,the VMC-4000H is an ideal alternative to massive double-column machining centers,with its net size of 10,000mm(L)x 4,000mm x 2,800mm.
Among the machine's special features are a screw-type chip conveyer for swarf removal,a gear rack mechanism connected to a servomotor to provide a rapid 30m/min traverse feed rate;a direct-drive spindle mechanism enabling high-speed turning without noise,backlash and vibration;and an umbrella-type automatic tool changer(ATC)for short-distance changing.
Chiang claims that the effects of the global economic slowdown on his company have been minimal."The impact has been particularly severe for manufacturers of standard machines in large volumes,"he explains,"but not for manufacturers like us,who make dedicated-purpose machines in small volumes for a wide range of customers."He adds that companies like his own are much more nimble in the market than big suppliers of mass-market machines.
Source:
http://www.cens.com/cens/html/en/news/news_inner_41259.html