Most Taiwanese printing machinery suppliers experienced downturns during the first half of 2012 due both to global economic uncertainty and a growing rivalry between emerging competitors.
According to the latest data issued by the Taiwan Association of Machinery Industry(TAMI)on its website,the industry`s exports as of the end of April totaled US$6.888 billion,up a moderate 3.3%from US$6.669 billion a year ago.However,in some sectors such as plastics and rubber machines,textile,and papermaking and printing machines,exports shrank.
The papermaking and printing machine sectors,contributing 4%of the total of the industry`s exports,exported US$272.671 million,down 5.8%from US$289.591 million a year earlier,according to TAMI.Insiders have attributed the declining export orders mostly to the sluggish global economy impacted by both the lingering debt crisis in the EU bloc and economic slowdowns in the United States and emerging countries,and have a mainly pessimistic view of the worldwide market for the second half of the year.
Widespread export declines in Taiwan have led some local printing machine makers to strive to stay afloat by concentrating on enhancing their technologies,which has resulted in new and cutting-edge machines.
Fu Kuang
Fu Kuang Industrial Co.,Ltd.is one such company.A professional supplier of various printing machines and related auxiliary equipment,it was founded in 1974 by President C.C.Yu.Yu devised his first sealing and cutting machine for PE(polyethylene)and PP(polypropylene)bags in 1963,and the company has become well-known in the sector in Taiwan`s central city of Taichung.
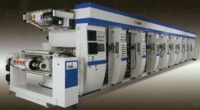
Few would question that Yu is one of Taiwan`s most eminent engineers of printing machines,having succeeded in designing Taiwan`s first lubrication-free system that became an integral part of his company`s sealing and cutting machines and led it to explore overseas markets.Yu`s technological achievements also include creating the photocell controller used in sealing and cutting machines,the Central Impression(CI)Flexographic printing press,and the full servo-controlled rotogravure printing press,all of which are local pioneering models.
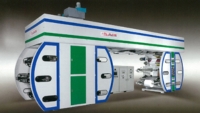
It is not an understatement to say that Yu`s achievement is the result of his conscientious pursuit of technological excellence.Three decades ago as the company`s president,he decided to move from bag making machines into printing and packaging-related machines.He and his R&D team absorbed trend-setting technologies from Japan and researched physical properties of ink and related materials,the development of different products,and improving the performance of its machines.
Yu said that his company is advancing towards sustainable development by extensively applying computer software to mechanical designs and has built automation technologies into its printing machines.Thanks to its consummate know-how,the company boasts nearly all of its needed parts and components,such as ink viscosity controllers,that can be made in-house to ensure the consistent quality of its machines."Fu Kuang successfully competes globally on the basis of technology and quality,"Yu said."We aim to position the image of MIT(made-in-Taiwan)in the upper echelons of printing machine suppliers in the world."
Currently,the company supplies a variety of photogravure printing,plastic bag making and precision plate mounting machines,Web guiding systems,and tension,ink viscosity and automatic color controllers,most of which are exported to food and beverage packagers.
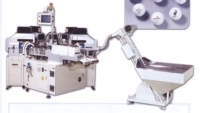
Flexographic Printing Press
The launch of the FKF series CI Flexographic Printing Press is a result of Fu Kuang`s continuous efforts to improve its technology.Yu said that packagers are increasingly using flexographic printing machines to replace conventional rotogravure,lithographic and screen printing models and that this has a variety of benefits such as lower costs,higher efficiency,easier maintenance,improved standardized parts and auxiliary equipment,and becoming even more user and eco-friendly.With more than 20 years of experience in flexographic printing technology,the company has gained advantages over its competitors,Yu said.
Yu said that the flexographic machine utilizes CI to achieve better color registration,and that the materials to be printed are supported by the cylinder and a hot wind dryer combined with an automatic temperature controller.A separated electric box allows for safer operation and more consistent output.
In addition,the doctor blade is chambered for high-speed printing,and the transmission system is driven by a high performance AC motor along with a digital frequency inverter.Also,the encoder buttons are designed both on the control chassis and body for convenient operation.Color registration and plate mounting are easy to adjust and are controlled by buttons.
For better utility,the machine has auxiliary equipment options that include plate cylinders of various sizes,unwind and rewind web guiding systems,ink viscosity regulators,printed graphics inspection systems,ceramic anilox rollers and air compressors.
"In the future,flexographic printing will become part of the industry mainstream,"Yu said."Our company has focused on developing such machines,and we have phased in larger-sized CNC machining centers in production to enhance output and quality.With strong technologies we can compete very well with our Chinese rivals in a challenging market."
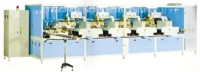
Guger
Founded in 1987 in New Taipei City in northern Taiwan,Guger Industries Co.,Ltd.focuses on printing machines and considers improving its technology to be the company`s bread and butter,said President Chen Tien-shong,who has more than three decades of experience with printing machines.
Guger offers a wide range of printing machines and related peripherals that include auto cap pad printing machines,4-color screen printing machines,5-in-1 combination pad printer machines,SMT printing machines,hot stamping and thermo-transfer printing machines,dryers,automatic dispenser machines,contact lens printers,vacuum heat transfer machines,specialty printers for LCD and photoelectric industries,golf ball printers,bottle printers,coin printers,and printing plate and stencil making equipment,all of which have been distributed worldwide under its brand Guger to countries such as Malaysia,Singapore,Burma,Vietnam,the Philippines,Egypt,Saudi Arabia,Brazil,the United States,Argentina and China.
The company,which indirectly has become part of the supply chains of Taiwan`s heavyweight electronic companies such as HTC,Quanta Computer,Hon Hai Precision Industry and Catcher Technology,has been affected by the faltering markets for 3C(computer,communication and consumer electronics)and high-tech electronic products so far this year,Chen said.
"It is notable that although in-mold lamination machines are one of our strengths,competition among Asian suppliers has been intensifying over the past two years,"Chen said.He said that Taiwanese printing machine suppliers are likely to be overwhelmed in the global market unless they use advanced automation technology to upgrade their machines.
Automatic Printers
In recent years,Guger has focused on developing automatic printers for different industries such as 3C,medical instruments,sport goods and foods,Chen said.It has also worked closely with local R&D bodies,such as Industrial Technology Research Institute,to improve its images and capability and achieve market diversification to survive in an increasingly competitive global market.
The company`s topmost product is its WE4-400TR Automatic Universal Screen Printing Machine.The machine features use of improved automation technology to capably print 3,600 bottles of all kinds of shapes per hour and produce 4-color printings."This high performance printing machine was created from our concentration on automation technology and has been well received among beverage packagers worldwide,"Chen said.
Another of Guger`s products that underlines its technological competitiveness is the WE-9159-1 10-color Golf Ball Printer.A programmable operation display controls the servo motor index and allows the in-feeding system to be switched to a single or double mode,and a special rotary device ensures precise color registration.Both of these features help to make the machine more energy efficient.
This printer also includes the following features:use of a high-quality sealed ink cup made in Germany for more stable and precise printing;a beefed-up hot air dryer to speed up drying time;a larger plastic feeder with effective projection designs to prevent balls from being damaged and scratched when fed;and extra light mounting for clearer printing.Chen said the ball printer can produce 3,600 pieces of five-color,two-side printings with the double in-feeding and double out-feeding systems hourly,and 1,800 pieces of 10-color,single-side printings with single in-and out-feeding systems,the fastest printing speed in Southeast Asia.
"Thanks to our dedication to advanced research on new technologies,our printing machines have been sought after by high-tech companies worldwide,including Kinston that has recently used our machine to print micro SD cards,"Chen said."Moreover,Guger is also one of ITRI`s assistant suppliers for its whole-plant solutions that are supplied overseas.All of this shows that our company has remained ahead of most of our peers in terms of technology."
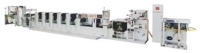
Labelmen
With global warming getting worse,Labelmen Machinery Co.,Ltd.is devoted to achieving environmental sustainability by using green,renewable material that promotes energy efficiency and eco-friendliness.This is how Labelmen builds up its new generation label printing machines to be compatible with green printing.
Labelmen,founded in 1965,is today a renowned brand name in the printing industry.With a history of more than 40 years,Labelmen has successfully sold its high quality printing machinery all around the world.The newly launched RS-350PS(Alan Type)Multi-functional Full Rotary/Intermittent Offset Printing Machine is designed and manufactured in line with the concept of green printing to meet customers'demands.
The company claims that this machine is equipped with the Ani-Print Anilox Inking System to meet not only the current,but also future market trends,and features the Quick Make-Ready specially for short-run jobs that can achieve up to 60%of time savings and the usage of Full Servo Control,which makes this machine able to generate 90%less waste than competing models.
The machine still has lots of other key advantages,including higher productivity for both short and long-run jobs,superb CMS(Color Management System)and Ani-Print Anilox Inking for consistent,high printing quality,quick and easy reproduction on printing,UV Ink application,full integration workflow and Production Job Management System to ensure the ultimate in user-friendly technology.
The company states that the RS350PS(Alan Type)Multi-Functional Rotary/Intermittent Offset Printing Machine is customers'solution provider,cost controller,innovation partner and growth maximizer.
Source:
http://www.cens.com/cens/html/en/news/news_inner_41258.html